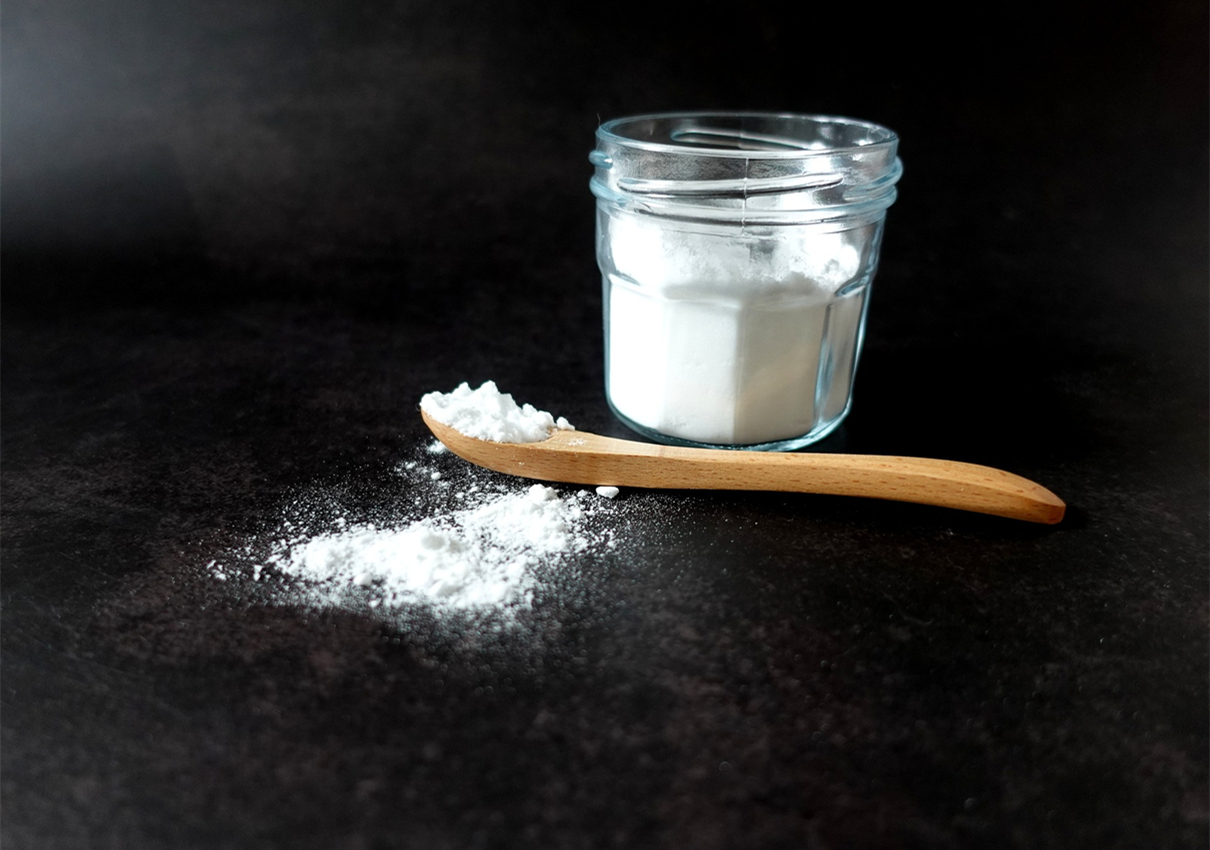
We have 6 series PVDF products which could be applied on various industries.
DY-1 is a kind of fine powder PVDF product, which could be blended with acrylic resin and other additives to form high performance PVDF fluorocarbon coating material. This coating material based on DY-1 PVDF has good mechanical strength, tensile strength, resistant ability to UV light and bad climate condition. The technical data is as below.
Item | Value | Test Method |
---|---|---|
Shape | White Powder | Eye |
Purity | ≥99.5% | PVDF |
Solubility | Solution is clear without impurity | 30℃, 1hr, 1g/10ml NMP |
Fineness | ≤25um | ASTM D1210 |
Melt mass flow rate | 0.5-1.0g/10min | ASTM D1238(230℃, 10kg) |
Density | 1.74-1.77g/cm3 | ASTM D792 |
Melting Point | 155-168℃ | ASTM D3418 |
Moisture Content | ≤0.1% | Loss on Drying |
Thermal Decomposition Temperature | 383-393℃ | TGA(1%, AIR) |
Stormer Viscosity | ≥90 | Ku |
Yellowing Resistance | Close to sample | ASTM D1148 260℃ 1hr |
DY-1 is a kind of fine powder PVDF product, which could be blended with acrylic resin and other additives to form high performance PVDF fluorocarbon coating material. This coating material based on DY-1 PVDF has good mechanical strength, tensile strength, resistant ability to UV light and bad climate condition. The technical data is as below.
Item | Value | Test Method |
---|---|---|
Shape | White Powder | Eye |
Purity | ≥99.5% | PVDF |
Solubility | Solution is clear without impurity | 30℃, 1hr, 1g/10ml NMP |
Fineness | ≤25um | ASTM D1210 |
Melt mass flow rate | 0.5-1.0g/10min | ASTM D1238(230℃, 10kg) |
Density | 1.74-1.77g/cm3 | ASTM D792 |
Melting Point | 155-168℃ | ASTM D3418 |
Moisture Content | ≤0.1% | Loss on Drying |
Thermal Decomposition Temperature | 383-393℃ | TGA(1%, AIR) |
Stormer Viscosity | ≥90 | Ku |
Yellowing Resistance | Close to sample | ASTM D1148 260℃ 1hr |
Item | Value | Test Method |
---|---|---|
Shape | White Powder | Eye |
Solubility | Solution is clear without impurity | 30℃, 1hr, 1g/10ml NMP |
Rotary Viscosity | ≥0.45PaS | 0.1g/ml DMAC |
Intrinsic Viscosity | 1.6-1.9 102ml/g | Arrhenius Viscosity Formula |
Melting Point | 160-170℃ | ASTM D3418 |
Moisture Content | ≤0.1% | Loss on Drying |
Item | Value | Test Method |
---|---|---|
Shape | White Pellet | Eye |
Melt mass flow rate | 10-25g/10min | ASTM D1238(230℃, 12.5kg) |
Yellowing Resistance | Close to sample | ASTM D1148 260℃ 1hr |
Tensile Breaking Strength | ≥25MPA | ASTM D638, GB/T1040.1 50mm/min@23℃ |
Elongation at Break | ≥20% | Same as above |
Yield Tensile Strength | ≥25MPA | Same as above |
Elongation at Yield | ≥10% | Same as above |
Density | 1.77-1.79g/cm3 | ASTM D792 |
Melting Point | 165-170℃ | ASTM D3418 |
Hardness | 74-80 Shore | ASTM D2240 |
Item | Value | Test Method |
---|---|---|
Melt mass flow rate | 6-26g/10min | ASTM D1238(230℃, 5kg) |
Yellowing Resistance | Close to sample | HG/T 3862-2006 |
Tensile Breaking Strength | ≥30MPA | ASTM D638, GB/T1040.1 50mm/min@23℃ |
Elongation at Break | ≥20% | Same as above |
Yield Tensile Strength | ≥40MPA | Same as above |
Elongation at Yield | ≥20% | Same as above |
Density | 1.77-1.79g/cm3 | ASTM D792 |
Melting Point | 165-171℃ | ASTM D3418 |
Hardness | 74-80 | ASTM D2240 |
Moisture Content | ≤0.025% | Loss on Drying |
Thermal Decomposition Temperature | ≥410℃ | ASTM D3418 |
Item | Value | Test Method |
---|---|---|
Solubility | Solution is clear without impurity | 30℃, 1hr, 1g/10ml NMP |
Rotary Viscosity | 7000-10000mPaS | 0.1g/g NMP 30℃ |
Molecular Weight | 0.7m to 0.9m da | GPC |
Melting Point | 162-172℃ | ASTM D3418 |
Enthalpy of Melting | 35-44J/g | ASTM D3418 |
Glass Transition Temperature | -40oC | DMTA |
Modulus | 1600-1800Mpa | ASTM D637 1mm/min |
Yield Strength | ≥40-50MPA | ASTM D638, GB/T1040.1 50mm/min@23℃ |
Breaking Strength | ≥34-49MPA | Same as above |
Elongation at Yield | ≥5-10% | Same as above |
Elongation at Break | ≥50-250% | Same as above |
Moisture Content | ≤0.1% | Loss on Drying |
Iron ion | <40ppm | JY/T015-1996 |
Volume Conductance | >1*1014 Ohm.cm | ASTM D257 DIN 53483 |
Limit Oxygen Index | 44% | ASTM D2863 |
DY-9002 is a kind of PVDF homopolymer with low melt mass flow rate, belong to thermoplastic fluoropolymer. DY-9002 PVDF resin has good thermostability, mechanical strength, abrasive resistance, resistance to acid, alkali, strong oxidizer and halogen. It is steady on most of chemical agent and is suitable for making Li-ion battery binder. Hydrogen fluoride would release from DY-9001 PVDF polymer when the temperature is higher than 300℃. The technical data is as below.
Item | Value | Test Method |
---|---|---|
Solubility | Solution is clear without impurity | 30℃, 1hr, 1g/10ml NMP |
Rotary Viscosity | 10000-15000mPaS | 0.1g/g NMP 30℃ |
Molecular Weight | 0.9m to 1.1m da | GPC |
Melting Point | 162-172℃ | ASTM D3418 |
Enthalpy of Melting | 35-44J/g | ASTM D3418 |
Glass Transition Temperature | -40oC | DMTA |
Modulus | 1600-1800Mpa | ASTM D637 1mm/min |
Yield Strength | ≥40-50MPA | ASTM D638, GB/T1040.1 50mm/min@23℃ |
Breaking Strength | ≥34-49MPA | Same as above |
Elongation at Yield | ≥5-10% | Same as above |
Elongation at Break | ≥50-250% | Same as above |
Moisture Content | ≤0.1% | Loss on Drying |
Iron ion | <40ppm | JY/T015-1996 |
Volume Conductance | >1*1014 Ohm.cm | ASTM D257 DIN 53483 |
Limit Oxygen Index | 44% | ASTM D2863 |
Other fluoropolymer products
PTFE, FEP, PFA and ETFE
PTFE granular fluoroplastics are ideal for compression molding a wide variety of components and shapes; such as rods, tubes and sheets. Products fabricated from genuine PTFE are unaffected by most chemicals and feature superior electrical, low friction and mechanical properties.
Products manufactured with genuine Everflon® PTFE are rated for continuous service at 260°C (500°F).
Everflon® PTFE granular fluoroplastic resins are considered non-melts and are generally converted to finished articles in a three step process.
1) The resin is compression molded into a shape form (rod, tube, sheet).
2) The shape, once removed from the mold, is then sintered above its melting point to form a solid PTFE billet.
3) The solid PTFE billet is then machined into the finished article.
FEP (fluorinated ethylene propylene) is a melt processable fluoroplastic. FEP can be used in applications that don’t require the enhanced properties, and temperature rating of PFA.
FEP fluoroplastics are processed by conventional melt extrusion techniques and by injection, compression, transfer and blow molding processes. FEP fluoroplastics are ideal for wire coating and molding a wide variety of end use articles and components.
FEP offers an excellent combination of properties characteristic of all fluoroplastics; a wide service temperature range, exceptional dielectric and electrical properties, low coefficient of friction, low flammability and chemical resistance. FEP has a service temperature range, up to 200°C (392°F).
While FEP can be fabricated into solid shapes and molded articles it is best known as an industry leading product line in the wire and cable industry where it is used for wire coating and cable jacket fabrication. FEP offers wire and cable OEMs a high performance fluoroplastic material with excellent electrical properties, ease of processing and consistent performance.
The FEP product line is one the broadest in the industry. With Melt Flow Rates (MFR) from 3 to 30, and a wide range of application specific grades, FEP is uniquely positioned to offer exceptional performance in both general purpose and high speed wire and cable constructions.
PFA (perfluoroalkoxy) fluoroplastics are available in pellet or powder form, and combine the processing ease of conventional thermoplastic resins with the high performance properties of PTFE.
PFA fluoroplastics are processed by conventional melt-extrusion techniques and by injection, compression, rotational, transfer and blow-molding processes. PFA fluoroplastics are ideal for wire coating and molding a wide variety of end use articles and components .
Products fabricated from genuine PFA are unaffected by most chemicals and feature superior electrical, low friction and mechanical properties and offer a wide service temperature range, up to 260°C (500°F).
PFA provides superior creep resistance at high temperatures, excellent low temperature toughness and exceptional flame resistance. Special grades of PFA (E series) have been developed to meet the rigorous demands of the semiconductor industry for purity, low extractable levels and minimal outgassing.
Additional grades of PFA are available to support roto molding and other specialty applications.
ETFE (ethylenetetrafluoroethylene) is a melt processable fluoroplastic resin. ETFE fluoroplastics are ideal for wire coating and molding a wide variety of end use articles and components. ETFE has a wide service temperature range with characteristics of other fluoroplastic resins; low flammability, chemical resistance, exceptional dielectric and electrical properties, superior mechanical toughness, abrasion resistance and environmental robustness.
ETFE fluoroplastic grades have a service temperature range of 150°C- 200°C. In addition to these upper service temperature ranges, ETFE also retains its useful properties at cryogenic temperatures.
While ETFE can be fabricated into solid shapes and molded articles it is best known as an industry leading product line in the wire and cable industry where it is used for wire coating and cable jacket fabrication. ETFE offers wire and cable OEMs a high performance fluoroplastic material with excellent electrical properties, ease of processing and extreme toughness.
The ETFE product line is one the broadest in the industry. With Melt Flow Rates (MFR) from 2 to 30, and a wide range of application specific grades, ETFE is uniquely positioned to offer exceptional performance in both general purpose, thin wall and wire and cable constructions.
Special ETFE grades are also available for special applications involving rotational molding and where static dissipative or adhesion properties are required.
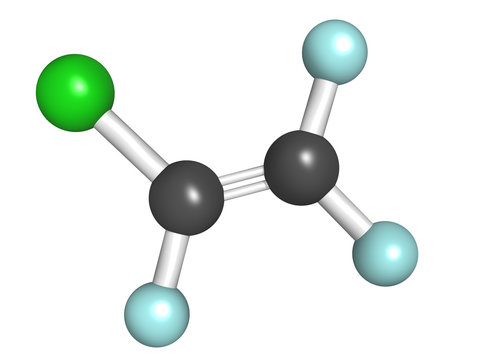
New Product PCTFE.
PCTFE has high tensile strength and good thermal characteristics. It is nonflammable and the heat resistance is up to 175 °C. It has a low coefficient of thermal expansion. The glass transition temperature (Tg) is around 45 °C.
PCTFE has one of the highest limiting oxygen index (LOI). It has good chemical resistance. It also exhibits properties like zero moisture absorption and non wetting.
It does not absorb visible light. When subjected to high-energy radiation, it undergoes degradation like PTFE. It can be used as a transparent film.
The presence of a chlorine atom, having greater atomic radius than that of fluorine, hinders the close packing possible in PTFE. This results in having a relatively lower melting point among fluoropolymers, around 210–215 °C.
PCTFE is resistant to the attack by most chemicals and oxidizing agents, a property exhibited due to the presence of high fluorine content. However, it swells slightly in halocarbon compounds, ethers, esters and aromatic compounds. PCTFE is resistant to oxidation because it does not have any hydrogen atoms.
PCTFE exhibits a permanent dipole moment due to the asymmetry of its repeating unit. This dipole moment is perpendicular to the carbon-chain axis.
Series | Melt Flow Index | Usage |
MPC-100 | ≤3 | Sealing Product |
MPC-300 | 3±1 | Sealing Product Extrusion Molding |
MPC-500 | 5±1 | Extrusion Molding Thin Film |
MPC-700 | 7±1 | Thin Film |
MPC-900 | ≥9 | Thin Film |
Item | Value | Test Method |
Density | 2.11-2.16g/cm³ | ASTM D792 |
Crystallinity | 40-80% | |
Molding Shrinkage | 0.015-0.020cm | 30℃, 1hr, 1g/10ml NMP |
Refractive Index | 1.425 | ASTM D542 |
Water Absorption | 0.00% | ASTM D570(24hr) |
Specific Heat | 0.22Cal/g/℃ | |
Thermal Conductivity | (4.7~5.3)X10-4 Cal/sec/cm2 | ASTM C117 |
Linear Expansion Coefficient | (4.5~7.0)X10-5℃/cm | ASTM D696(23-60℃) |
Melting Point | 210-212℃ | ASTM D3418 |
Z. S . T. | 200-300 Sec. | ASTM D1430 |
Tensile Strength | 31.4~37.2Mpa (320~380) (kgf/cm2) | ASTM D638 |
Elongation Rate | 50-200% | ASTM D638 |
Bending Strength | 67.6~72.5Mpa (690~740) (kgf/cm2) | ASTM D790 |
Compression Strength | 11.8~13.7Mpa (120~140) (kgf/cm2) | ASTM D695 |
Tensile Rebound Rate | (13~15)X103Mpa | ASTM D638 |
Compression Rebound Rate | (14~16)X102Mpa | ASTM D695 |
Bending Spring Rate | (16~19)X102Mpa | ASTM D790 |
Impact Strength | 2.5~3.5Ft-1b/in | ASTM D256 |
Hardness | 85-95Shore | ASTM D676 |
Bearing Deformation | 0.2% | ASTM D621 |
Permittivity | 60Hz 2.24-2.8 103Hz 2.3-2.7 106Hz 2.3-2.5 | ASTM D150 |
Dielectric Loss Factor | 103Hz 0.023-0.027 | ASTM D150 |
Dielectric Breakdown Strength | 12Kv/0.1mm | ASTM D149 |
Surface Arc Resistance | >360Sec | ASTM D495 |
Volume Intrinsic Resistance | >1016Ohm-cm | ASTM D257 |
Surface Intrinsic Resistance | >1014Ohm | ASTM D257 |
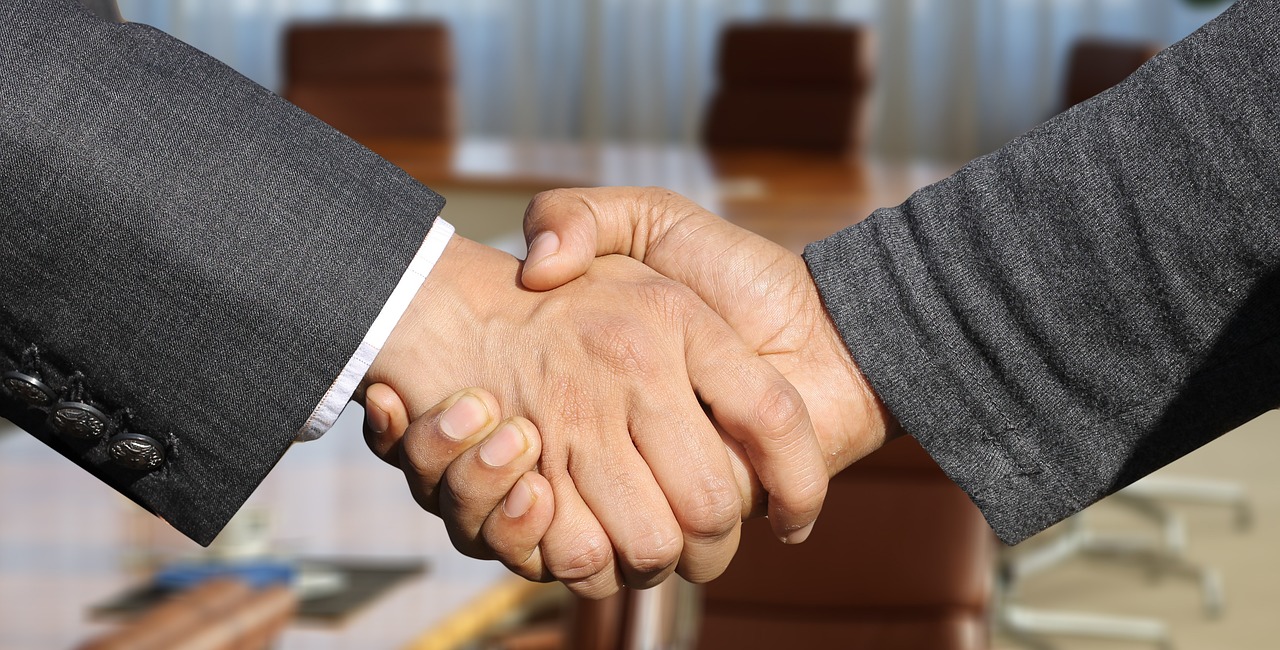
Office location
Unit 301, No.1 Buildling Wanxiang International BusinessCenter,No.1690 Gangzhong Road, Xiamen, China
Factory location
Nanshou Industrial Park, Linyi Couty, Dezhou, China
Contact us
Tel: 86 13860113054
Email: sales@toppvdf.com
Let’s collaborate!
Send to email sales@toppvdf.com or filled the belowed form to contact us.